introduction
With a bold plan that imports expertise from a highly efficient Nordic model, Hudson Square Properties (HSP) is looking to fully decarbonize their commercial building portfolio—starting with 345 Hudson.
While novel for the U.S. market, the HSP roadmap utilizes thermal networking techniques vetted across decades in other regions. Rather than rely on the innovation of new technologies, this approach innovates through design. In effect, the HSP innovation is in how they look at building systems—using familiar parts to create a unique, inexpensive, and highly efficient system to deliver the high-quality office environments that today’s tenants demand.
about the Empire Building Challenge
HSP is among the inaugural cohort of real estate partners convened by New York State Energy & Research Development Agency for their Empire Building Challenge, a public-private partnership with leading real estate groups to decarbonize New York’s existing building stock by designing and implementing innovative tall-building cold-climate retrofits, tackling systemic market barriers, and attracting the world’s top solutions providers to the New York market.
The challenge’s first cohort of partners collectively represent more than 130 million square feet of New York real estate, and a massive influence over regional energy demand. If fully retrofitted to HSP’s level of peak load reduction, the combined impact would enable New York City to shut down the Astoria 5 coal power plant.
In January of 2022, New York State Governor Kathy Hochul announced the awarding of $20 million to HSP and three other real estate partners for their innovative proposals for high-rise low-carbon retrofits. This profile explores how HSP’s 345 Hudson retrofit meets the EBC’s key objectives: significantly reducing building Energy Use Intensity (EUI), removing on-site fossil fuel combustion, producing a low-cost, high-value, replicable solution, engaging leading international solutions providers, and eliminating market barriers.
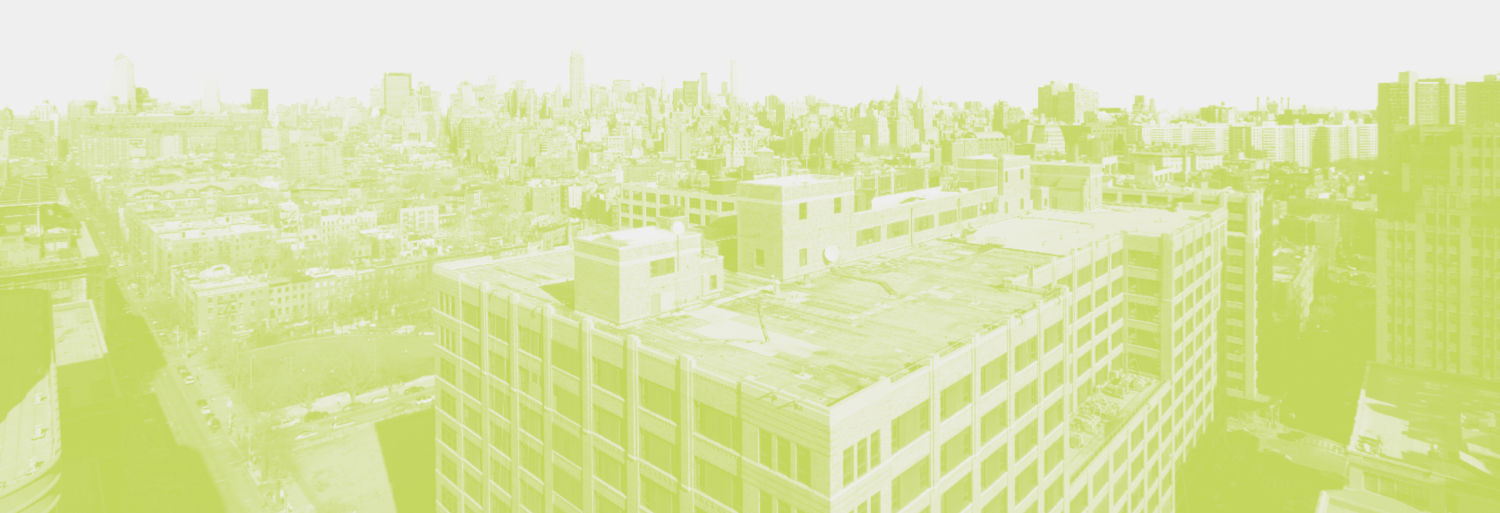
approach
The foundational innovation in HSP’s retrofit strategy at 345 Hudson is to see heat not as something to be ejected in summer and supplied in winter, but as a resource to be shared among different spaces year-round. For large portions of a typical year, many offices heat some spaces while simultaneously cool others, with separate heating and cooling systems working independently to add heat to the former and remove heat from the latter. The HSP model provides an integrated system that allows these spaces to share that heat—not just within an individual floor, but between different floors in the same building, and even between buildings, dramatically improving energy performance.
Importantly, HSP’s approach can be applied in phases on a floor-by-floor or tenant-by-tenant basis, working with rather than against the natural lease turnover cycle, spreading costs across the term of their project and taking advantage of already planned capital expenditures.
HSP’s design approach, dubbed the “Nordic model,” follows a circular systems philosophy, challenging designers to consider building systems comprehensively, rather than as individual elements, and identify opportunities to incorporate circular, regenerative, and resource-efficient processes. The strategy is common in Nordic countries, gaining traction through aggressive climate policy, high shares of renewable electricity generation, and deep market penetration of heat pump technology.
The Nordic approach, which takes advantage of the natural variability in heat across the different spaces of a building, can be applied to a range of building typologies and uses. For instance, data centers, often seen as a substantial energy use liability, could effectively become the primary heating source for a whole building, as waste heat is captured and redistributed towards floors in need of heating.
energy & carbon outcomes
As floors are phased in and more tenants take advantage of the thermal network, the amount of energy recycled across the building increases, incrementally improving the efficiency of 345 Hudson. By 2032, once fully implemented, whole-building energy use would be expected to drop by more than 50% to about 38 kBtu/sf— 80% lower than an average large New York City office building. Total building carbon emissions would fall 85%, with reductions increasing towards 100% as New York’s electric grid becomes fully renewable. Notably, post-retrofit peak heating and cooling loads would fall by 92 and 63% respectively, reflecting the significant benefits of capturing, sharing, and recycling heat.
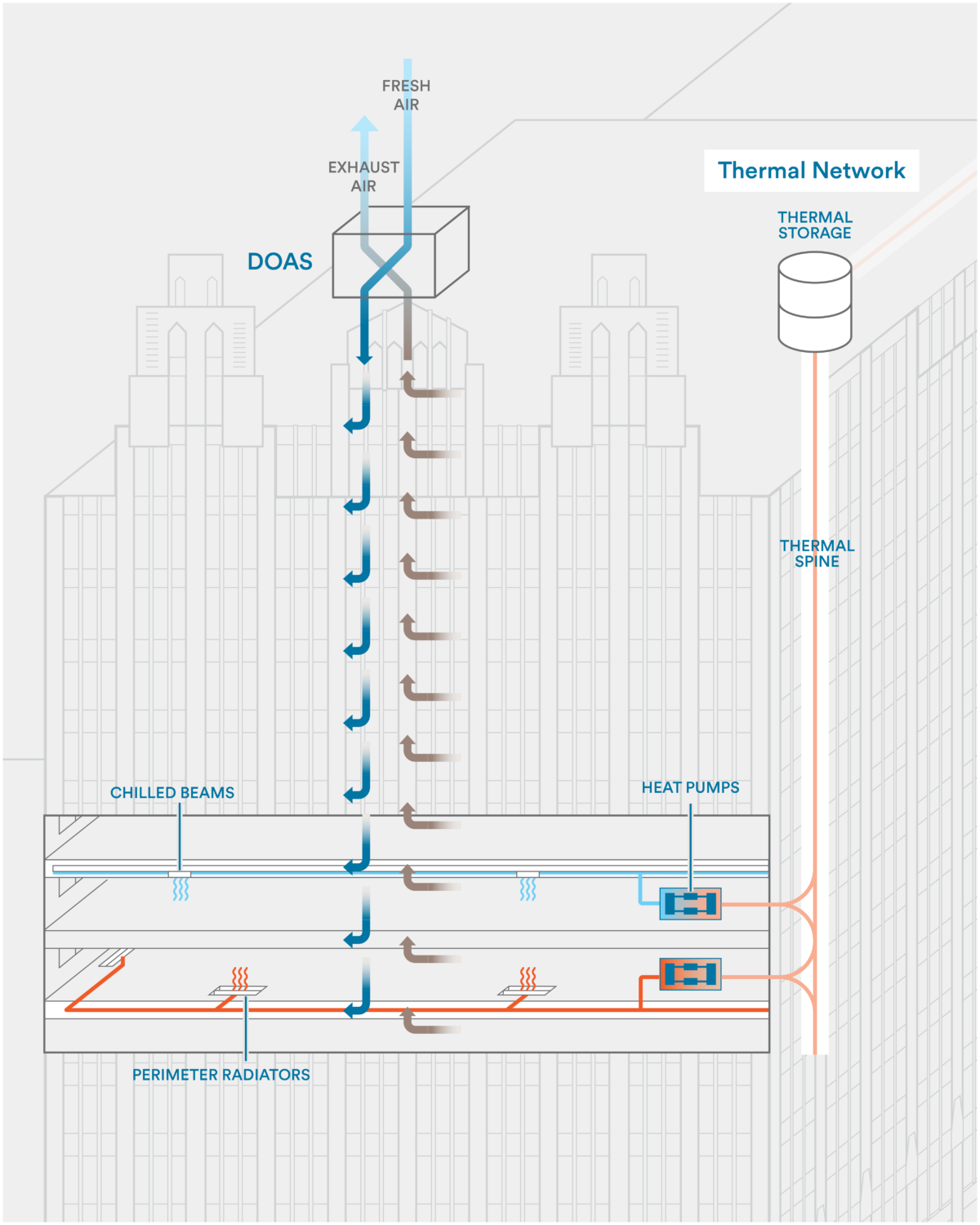
system innovations
The thermal network proposed for 345 Hudson consists of a repurposed condenser water loop, or thermal spine, running vertically from floor to floor. From this thermal spine, hydronic loops run outwards within each floor, allowing for efficient local energy exchanges between zones, using water as a medium. The result is a highly efficient, self-regulating network designed to reach a temperature close to the desired operative level by capitalizing on the natural variability in temperatures across zones and floors.
From this balanced state, floor-level water-source heat pumps, connected to thermal spine, cool or heat on demand, at critical junctures closest to the receiving zones. Note that the thermal network’s stable temperature range levels the playing field, providing a solid foundation for optimal heat pump operating conditions, relative to highly fluctuating outdoor temperatures.
Water will then be run through high-temperature active chilled beams, ceiling mounted heating/cooling coils supplied with water from the thermal network. Floors are conditioned as air flows across the coils. Low-temperature hydronic radiators connected to the thermal network provide additional heating and cooling capacity at the perimeters of each floor.
A high energy recovery Dedicated Outdoor Air System (DOAS) on the rooftop provides fresh air to the chilled beams, which induces additional airflow across the coils. Nearly 90% of the energy from exhaust air is recaptured and used to temper incoming air.
project team
Owner/Operator: Hudson Square Properties (Norges Bank, Trinity Church Wall Street, Hines)
Consulting Engineer: Urbs | Urban Systems
Heat Pump Manufacturer: Energy Machines
Engineer of Record: Jaros, Baum & Bolles
Thermal AI Integration: Noda
Transition Risk Insurance: Willis Towers Watson
Control Software: Modio
Energy Storage Analyst: Blueprint Power
Carbon Reduction Certification: International Finance Corporation
The road ahead
HSP’s 10-year deployment plan for 345 Hudson first targets improvements to the building’s core infrastructure, then phases in tenant retrofits, floor by floor. First, the primary air handling unit will be replaced with a high energy recovery DOAS system, followed by installation of the thermal spine and a building management system. As the project progresses floor by floor and use of the thermal network expands, heat pumps will supplant existing packaged terminal units. Updated floors will effectively become energy producers engaging in intra-floor heat exchange, rather than receivers of linear energy supply, benefiting the overall system.
Looking beyond 345 Hudson, HSP seeks to replicate the same set of solutions across their whole portfolio, a process that will see increasing returns to scale as local trades and service providers are familiarized with new technologies, international supply chains are strengthened, and innovative market actors enter the New York market—key objectives of NYSERDA’s Empire Building Challenge.
“You create an inherently smart system by following nature’s principles... then you add heat pumps.