About
MechoSystems HQ Renovation:
Pioneering daylighting provides the foundation for this comprehensive repurposing of MechoSystems’ former factory into a modern, LEED Gold corporate headquarters.
Process
The project began in 2009. In addition to the challenges a century-old building presents, MechoSystems continued to work in the building while the retrofit took place. These barriers were overcome by working with a strong team of engineers, architects, and consultants who determined early on that the phasing of the project should be system-by-system, rather than floor-by-floor as originally planned. The building was divided between east and west sides, and employees were housed in temporary office units in the building that shifted with construction. MechoSystems began by tackling all floors on the east side, which housed most of the building’s systems, including the bulk of the plumbing, electrical, and HVAC equipment. Upgrades included changing to a hot-water fin-tube radiation system, converting the boiler from steam to hot water, and installing gas-fired HVAC units on the roof. Additionally, an 180-kW emergency generator was installed, as well as a new server room with its own cooling system.The team had to bring its creativity to bear on structural and permit challenges as well. For example, it was critical for MechoSystems that the retrofit not dramatically alter the original feel of the building – with it’s open spaces and exposed structure. Maintaining that feel while meeting code sometimes required choosing a difficult and expensive option, such as developing a fire shutter system instead of building more interior walls.Retaining the building’s many large window openings, built when people in manufacturing worked mostly by daylight, was critical to the elevated atmosphere of the workspace. Significant effort was expended selecting windows and glazing that provided adequate thermal and UV protection while maximizing visible light. The lack of windows on the south side of the building was actually a benefit, since this dramatically limited solar heat gain, while other openings provided ample natural light for the workspaces.
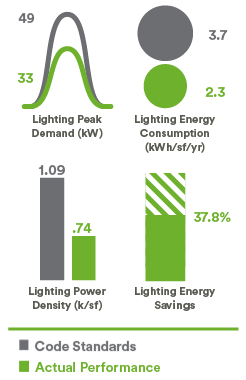
Facts about the building
Project type: Adaptive Reuse
Location: Queens, NYC
Year of project completion: 2013
Base building completed: 1918
Project size: 47,500 sf
Occupied during the retrofit? Yes
Existing Conditions
Built in 1918, the MechoSystems building was originally a mattress factory. At that time, electricity was expensive and not typically provided in all spaces. As a result, the building was designed to maximize daylighting, with large north, east, and west facing windows, as well as skylights and clerestory windows. The original design placed large manufacturing space in the basement and first floor, with very high ceilings, and lofted office space on the third floor. The heating system in place at the time of the retrofit was a steam boiler powered by heavy fuel oil. When Joel Berman, founder and CEO of MechoSystems, bought the warehouse in 1980, much of the heating equipment and layout were similar to the original design. As an architect, Joel was impressed by the natural daylight and opportunity that the space presented. Not only was it versatile enough to include both office and manufacturing spaces, it was accessible by public transportation and conveniently located near La Guardia airport, midtown tunnel, and the Queensboro Bridge into Manhattan. In the 1980s, MechoSystems invested about $1 million into piecemeal retrofits. Some were large projects, such as upgrading the boiler, putting in additional bathrooms, replacing the flooring and the roof, and installing double-paned windows. Others were less intensive but still added to the functionality of the space, such as removing interior walls and installing insulating plastic panels in the skylights to improve interior comfort. However, by 2004 the company’s needs had changed. Manufacturing was moved to New Jersey and Arizona in order to open up space to accommodate the growing staff. As their focus shifted toward controls, electronics, software development, and programming technology, MechoSystems wanted to create a space that mirrored its aspirations and showcased its technologies. MechoSystems used this major retrofit as a means to carefully adjust its culture to attract and retain high-level talent and to make a strong corporate statement about sustainability.
Design Conditions
Missing
Project Team
Project Owner
MechoSystems
Products & Installation
MechoSystems & Encelium
Incentive Provider
NYSERDA
Performance
In addition to creating a modern office that would reflect the high-tech aspirations of the company, MechoSystems wanted to demonstrate its commitment to sustainability by pursuing LEED Gold certification. This included installing solar PV, sourcing sustainable materials, and using green construction practices. Jan Berman, president of MechoSystems, saw the retrofit as “an opportunity to create a living laboratory, a showroom for our products, and an enhanced work environment.” Because the function of the building changed so dramatically (from mostly manufacturing to all offices), a direct comparison of pre- and post-retrofit energy use is not useful. To estimate the impact of its advanced systems on energy use, MechoSystems used computer-modeling to compare their actual energy use with a similar project that meets code, but lacks these controls. MechoSystems was able to significantly reduce both their total overall energy consumption and their peak demand for electricity, but here we will focus on the energy used by their lighting systems. Due to the daylighting and lighting controls implemented during the retrofit, MechoSystems’ was able to achieve impressive lighting energy savings. The lighting power density was scaled back from 1.09 W/sf to 0.74 W/sf, a 32% savings from the model and well below code. This helped reduce peak lighting demand from 49 kW to 33 kW, a savings of 33%, and their overall lighting consumption from 3.7 kWh/sf/yr to 2.3 kWh/sf/yr, a 37.8% savings.These reductions in energy use allowed the project to benefit from several NYSERDA incentive programs. The approval process for solar PV system incentives was simple and took less than three months. Other programs had a longer approval process of six to eight months, with funding received only after the systems were in place and specific performance criteria had been met.The company ensured that its employees were aware of these improvements by continuously monitoring energy usage and displaying it on dashboards throughout the building. Employees seem to really enjoy the additional daylight made possible by the advanced shading and lighting controls, and they have reported feeling more energized and productive during the day.
Benefits
- Maximizes use of daylight
- Increases lighting efficiency
- Overall energy consumption reduction
- Significant peak demand reductions
- Eligibility for NYSERDA incentives
- Increases occupant comfort and well being
Lessons Learned
The MechoSystems renovation was a constantly evolving project that benefited from foresight and creativity. Having a well-oiled team and an experienced project manager was crucial. The team learned early that to keep the building open during construction, a systems-based (versus an area-based) renovation approach was necessary. The team made sure to use the existing building advantages, such as availability of daylight, to maximize its energy savings and retain the character of the space. Additionally, this strategy reduced the amount of materials needed for the project. MechoSystems actively worked to prevent a “set it and forget it” attitude towards its advanced systems by continuously monitoring their energy use and making adjustments as needed.
Conclusion
The conversion from factory to office space was a visionary decision by the MechoSystems leadership. The company has produced an office headquarters that acts as a showroom for its products and services, and which has far more character than a standard office space. The design provides a place that enhances the well-being of staff, significantly reduces energy use, and allows for the continuous monitoring and optimizing of systems over time. The MechoSystems project demonstrates that repurposing older buildings, while a significant investment of time and money, can be extremely rewarding. Coupled with advanced systems, these spaces can be among the most comfortable available while also minimizing energy use.
“Our building was designed in the early 1900s, when electricity and lighting were far less efficient. So the building was specifically designed to maximize daylight. Our strategy was to utilize this original design as much as possible, but updated with the latest technology. The result is a delightful space that allows staff and guests a sense of the changing light and weather outside, while maintaining comfort and a fabulous work environment.