About
Partial occupancy of this Passive House certified residential building was achieved six months before final project completion through strategic timing of blower door tests.
early occupancy
The project team conducted multiple blower door tests to ensure the envelope would meet airtightness requirements, which cleared the way for early occupancy of the lower half of the building.
A successful guarded blower door test was conducted on two floors of the building in advance of a whole building blower door test, enabling a split temporary certificate of occupancy six months ahead of project completion. Coordinating multiple blower door tests required strategic construction sequencing that accelerated the completion of the building envelope’s airtight layer.
hands-on contractor training
The contractor team built a full scale mock-up on the construction site, which included a complete building envelope with window and door units and several corner conditions. The mock-up was used as a quality control and teaching tool for subcontractors who were able to practice and perfect high performance building techniques before applying them to the actual building.
maximizing square footage
A reduction in the overall thickness of the building envelope allowed for the maximization of floor area, creating functional interior spaces yielding the highest profit.
Flow Chelsea’s narrow lot proved challenging for the design team in laying out the interior spaces of the building. In order to maximize square footage, Aerated Autoclave Concrete (AAC) blocks were specified where Concrete Masonry Units (CMUs) would be used in typical construction. Compared to CMUs, AAC blocks offer equal compressive strength with much higher insulation capacity, allowing the architect to choose thinner exterior wall insulation without compromising performance.
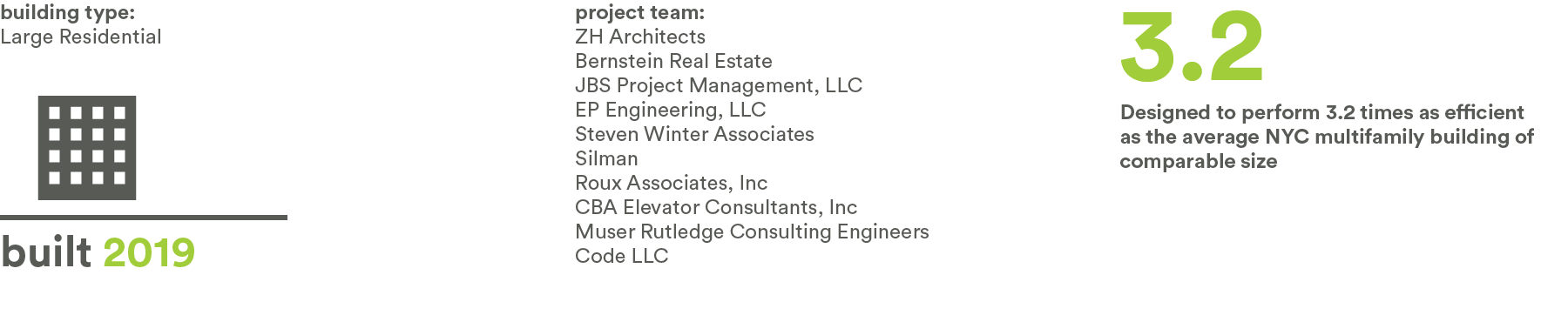