About
Park Terrace Gardens worked with an engineering firm to identify the most effective ways to reduce the co-op’s energy use and resolve chronic heating imbalances. Steam system measures included boiler, piping, venting, and control system improvements. These were supplemented with simple air sealing measures to minimize heat loss. The completed scope of work balanced building temperatures, improved comfort, and reduced heating fuel use by 19%, saving an average of $109,000 a year.
Process
Park Terrace Gardens is unique for having a “Green Committee,” made up of co-op members dedicated to increasing sustainability in the co-op’s five buildings. Leadership by the Committee, a generous financial incentive from NYSERDA, and a regulatory push from the City of New York were instrumental to getting this project off the ground.
In 2012, after participating in the NYC Clean Heat Program to convert the co-op’s five boilers from #6 fuel oil to cleaner burning #2 oil, members of the Park Terrace Gardens Green Committee contacted the engineering firm Bright Power to explore opportunities to make the co-op even more sustainable and energy efficient. The engineers analyzed the co-op’s five buildings and worked with residents and the onsite supers to create a scope of work designed to enhance comfort, improve steam system performance, and reduce overall energy use by 15% (thereby qualifying the co-op for a NYSERDA incentive covering 50% of the total project cost).
The completed steam system and air sealing measures resolved long-standing heating imbalances and inefficiencies, and yielded even greater savings that projected. The project reduced the co-op’s heating fuel use by 19%, saving an average of $109,000 a year.
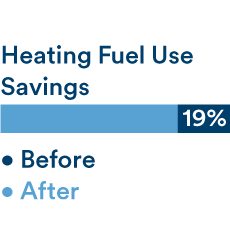
Facts about the building
Project Type: One-Pipe Steam Heating System Upgrade
Location: Inwood, NY
Project Completed: 2014
Base Building Completed: 1939
Project Size: 435,340 sf; 397 units; 5 buildings
Building Type: Multifamily Residential; Cooperative
Existing Conditions
Park Terrace Gardens’ one-pipe steam system was severely imbalanced, causing chronic overheating and eliciting regular complaints from residents. Air was not venting out of the steam distribution pipes efficiently, making it difficult for steam to reach the tops of the tall vertical riser lines. As a result, lower floors were being drastically overheated to allow steam to reach upper levels. Many residents reported leaving their windows open and radiator valves closed all winter to counteract overheating.
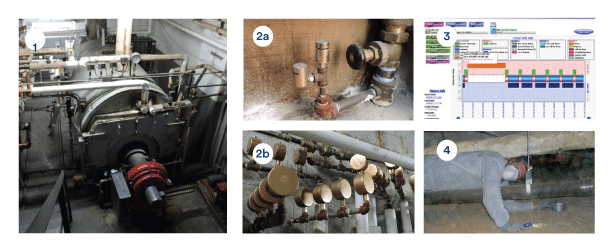
Green Features
1. Boiler & Burner Tune-Ups
Tuned boiler & burner, replaced gaskets, and installed back-of-boiler insulation
2. Master Venting
Installed high-capacity vents on riser lines (2a) and steam mains (2b)
3. Multi-Sensor Controls
Upgraded to internet-enabled controls with wireless temperature sensors.
4. Piping Improvements
Insulated bare piping & performed needed maintenance and repairs
Additional Measures (not pictured)
Installed A/C covers and weatherstripping
Project Team
Project Owner
Park Terrace Gardens, Inc.
Property Management
Douglas Elliman Property Management
Incentive Provider
NYSERDA MPP
Service and Installation
Bright Power, Inc.
Marlande Heating
Goldner Plumbing
Partners
- NYC Accelerator
Benefits
- Balanced flow of steam with more consistent and even heating to all apartments.
- Energy and fuel cost savings due to more efficient boiler and burner operation.
- Higher quality steam, with quieter pipes and radiators and improved equipment longevity.
- Greater ability to regulate boiler cycles and control building temperature.
- Increased resident comfort and satisfaction.
Lessons Learned
Project Approval: Winning co-op board approval was a major challenge. To allay the board’s concerns, the Green Committee (with technical guidance from the contractors and engineers) led a campaign to educate the board on the reasons for and benefits of the upgrades.
Resident Outreach: The co-op’s Green Committee, management team, and on-site supers worked with contractors to schedule in-unit work. The co-op worked with contractors known and trusted by residents, which made scheduling and arrange apartment access easier. The Green Committee also led an education campaign to keep residents informed about the upgrades, and sent thank-you notes after work was completed – a personal touch that made process more pleasant.
Technical Challenges: Contractors had difficulty accessing certain steam system components. In addition to pipes that were tucked away in tight crawl spaces, some radiators had irregularly shaped radiator cabinets or had furniture built over them, making them hard to reach. In a few cases, there was insufficient space to raise the radiator as needed for riser venting. Contractors had to devise alternative approaches, which slightly increased installation times and costs.
“This project made a huge difference – for years residents were resigned to being overheated. Now, we get far fewer heating complaints and are saving even more energy than expected.